We all know how tricky it can be when comes to using a Core Barrel Roller Bit. Using roller bit is not like using the bullet teeth, while bad welding work can make the whole expensive tools scrapped without even into the piling hole.
The following 7 points can help you weld and replace FIRMTECH roller bit confidently.
1. Cut the right gap
Cut gap on core barrel at proper dimensions, gap-width should not be left too big. Half to 2/3 height of cones should be out of barrel-top after welding. (for special soil formation, need adjust accordingly, contact to know more info.) Steel plates on two sides of the cones should be chamfered.
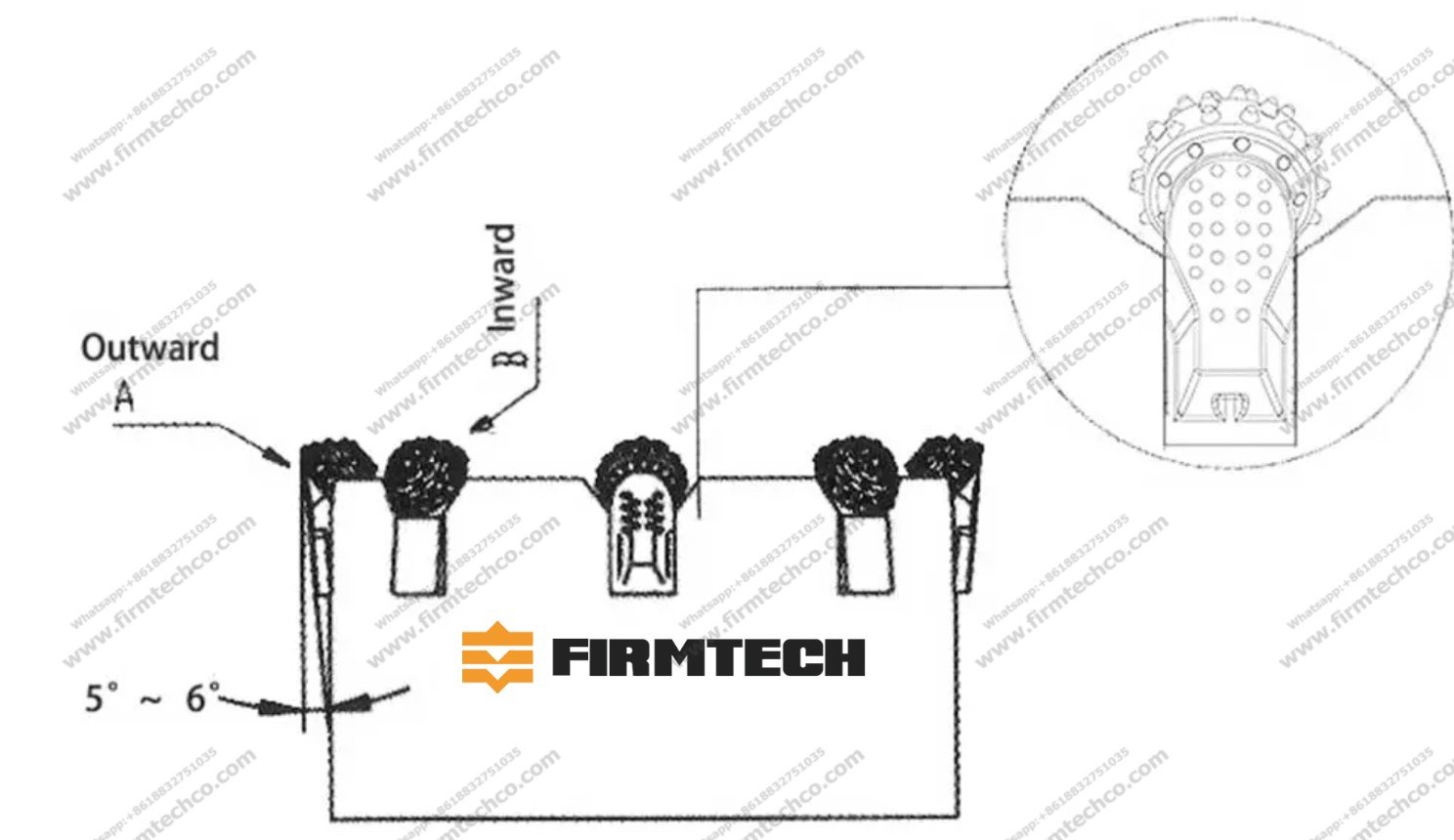
The half hide cone is mainly to protect the body snapped when piling extreme uneven formation. FIRMTECH has upgraded 4th Gen. Leg. check to get more accurate data.
2. Even numbers
Roller bit numbers in one core barrel should be even to facilitate the measurement of the diameter. Each pair of opposite roller bits distance shall keep the same. (for big dia, 2500mm above, some special design, the number can differ, contact to get suggested roller bit qty for each core barrel size )
3. Right angle
The angle of the welding roller bit should be position as 5-6 degrees. This is to protect the vulnerable shirttail place and maximize the cutting surface. (Important notice: different brand roller bit, its journal angle is different, this suggested angle positioned only work on firmtech roller bit. NEW upgraded Firmtech MH-1 & MH-3 no need worry welding angle, check for more info.)
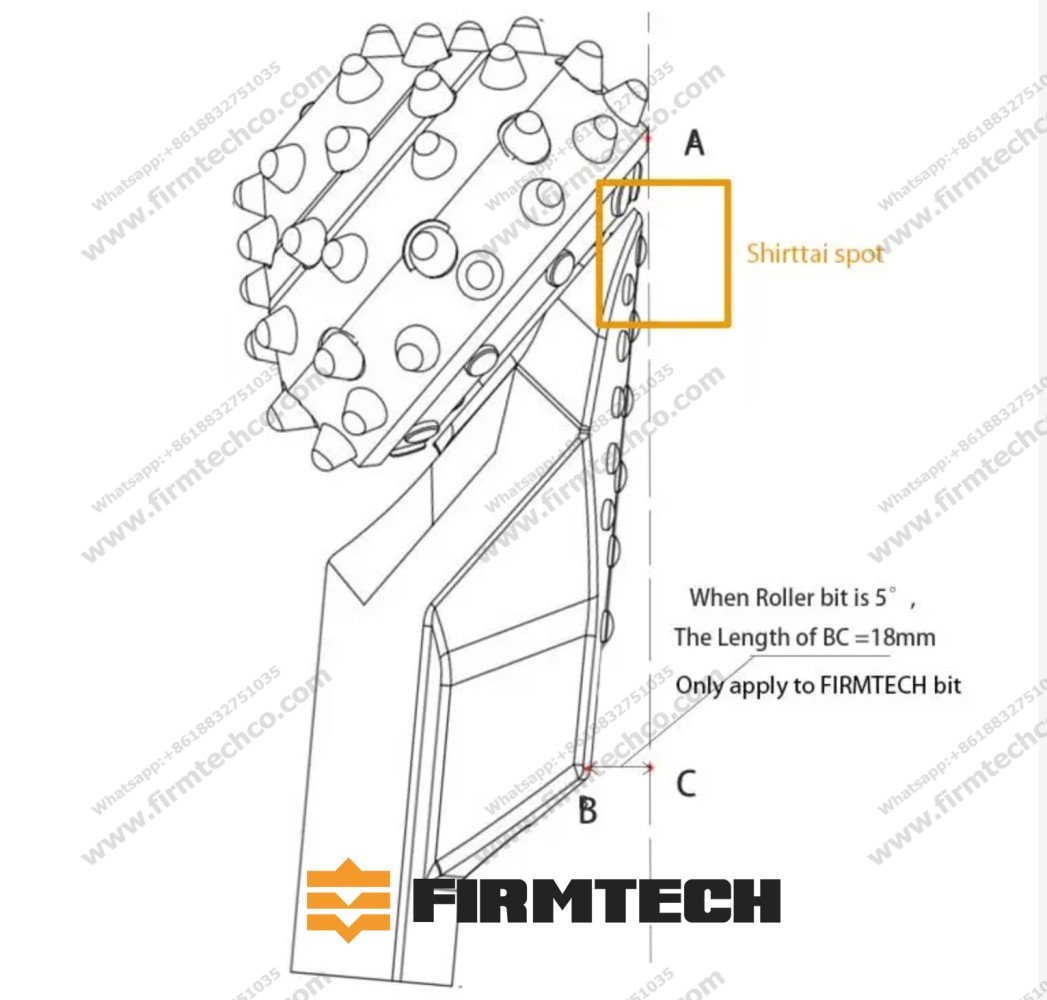
4. Same flat & circle
Keep all cones at the same height and same round circle, protruding roller bit will be broken easily.
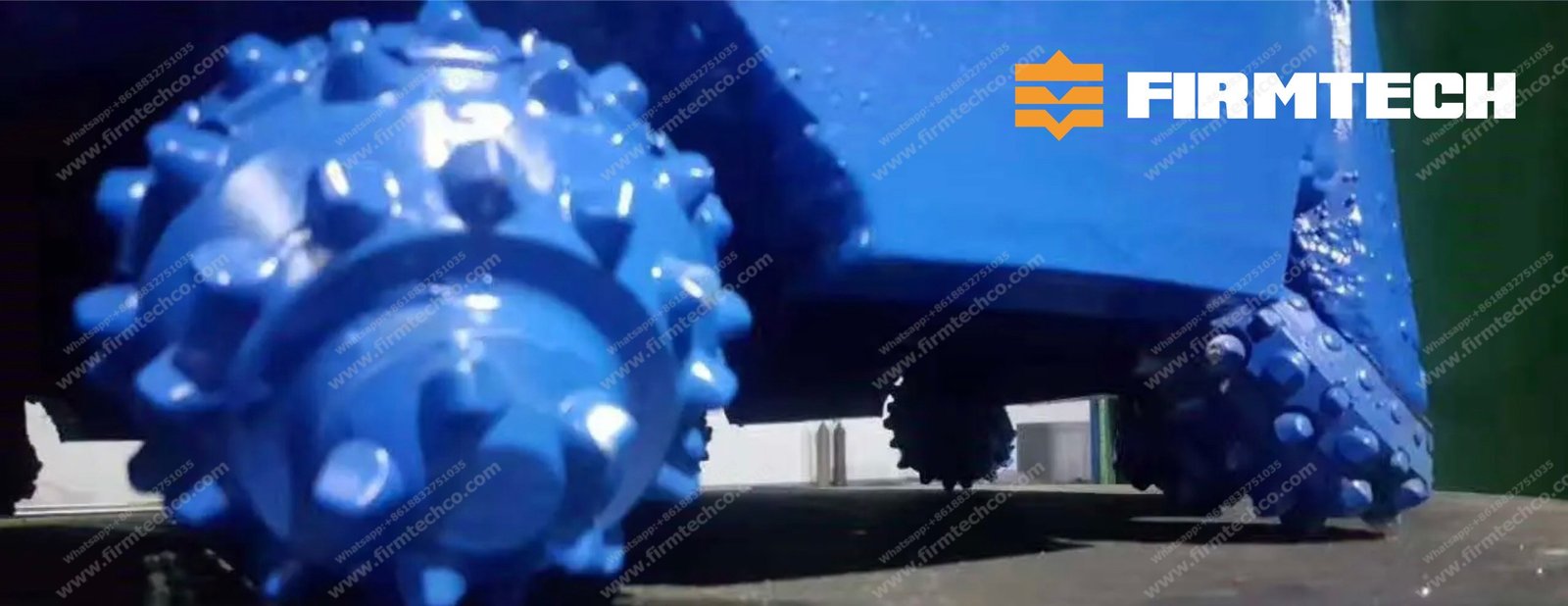
5. Right distance
The outward and inward roller bit should overlap to the right position ( the most outside point on the outward bit to the most inside point on the inside bit should be 120mm-140mm), otherwise, the inner circle of the roller bit will be worn out quickly.
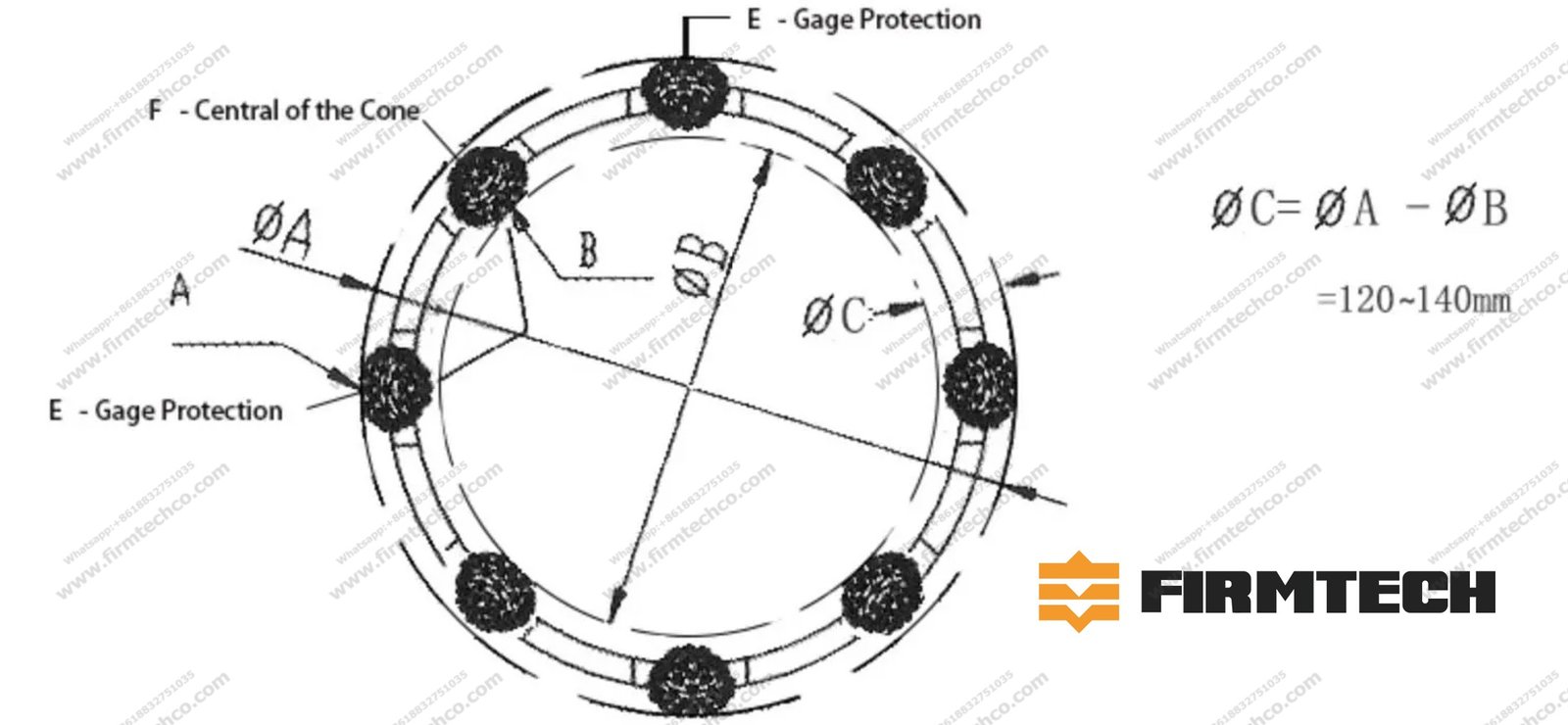
6. Cooling down
Put and cool roller cones in water, do not finish welding at a short time but by steps keep the temperature at a low level, especially cool the gap between arm and cone. High temperature may damage the seal O-ring or lubrication system.
7. Welding by steps
The roller bit should be welded evenly and slightly to fix the position, then apply the full welding, otherwise, the roller bits and angle will change.
If you are fabricating a roller bit core barrel, contact us to get detailed drawings for your spec. or more detailed roller bit welding instructions.
Firmtech focus on piling roller bit design and manufacturing, we offer one-stop solution, from roller bit quality control, welding work instruction, to operation suggestion. high penetration rate with ideal drilling cost in hard rock.